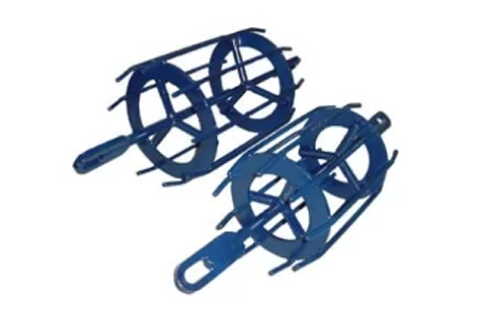
Deflection Testing
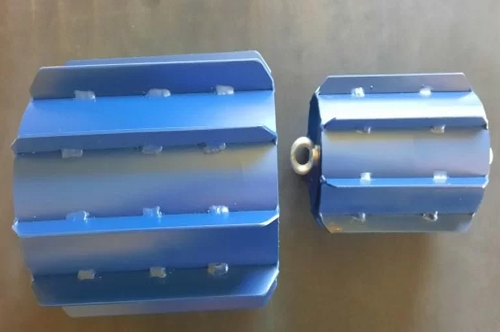
Why do we need Deflection Testing?
A pipe line or conduit which has deflection issues is weakened compared to a round pipe, line or conduit. Deflection may also lead to fracturing or cracking of conduit layers. A conduit that has deflection may have the squashing stresses removed to allow conduit to re-round, but this conduit will be more susceptible to future deflection than a new, round conduit. Early detection and correction of compaction issues is a must if the conduit is to be saved.
Prevention and good construction practice is a must as it is far cheaper to do it right the first time than enter into costly repairs. Most cases of deflection are due to incorrect supporting of the conduit, or a bed that is not uniformly structural, due to incorrect haunching and back-filling or excessive compaction in too thin a layer.
Deflection testing is generally a condition placed on a contractor by an authority or consultant to make sure that the pipeline has been installed correctly and has the best chance of longevity into the future and is usually part of a 'witness' or 'hold point' in the construction process.
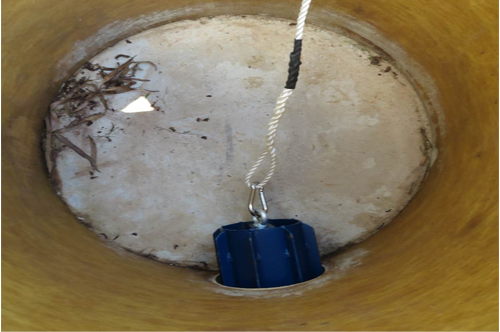
How is Deflection testing done?
Deflection testing or ovality mandril testing is done by pulling a verified proving tool through each section of pipeline using a rope attached on both sides so if the prover gets blocked or stuck it can be pulled back in the direction it came from.
Prover mandrels, or pigs used for inspecting pipelines consist of fins or arms along their length and are made to a specific size for each size of pipeline. They are made from steel, aluminum, plastic and urethane materials. The tool will be stopped if it encounters a squashed, deformed, blocked (by a pinched ring) or damage, it will stop. They generally push debris out of its way. A more modern approach is to use lasers or specialty video inspection equipment on tractors instead of pigs, mandrels and provers.
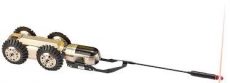